Hohe Zerspanraten allein sind kein Maßstab der Produktivität
1. Teil einer Artikelserie
Ingo Laqua, CIM Aachen GmbH
Der effiziente Einsatz von Maschinen und Anlagen im Produktionssystem ist für die Sicherstellung von Wirtschaftlichkeit und Flexibilität zwingend. Insbesondere gilt es, Anlagenkapazitäten für die marktsynchrone Produktion gezielt bereitzuhalten.
Heute gibt es noch immer Produktionsleiter, die voller Stolz vermelden, dass das neue Bearbeitungszentrum rund um die Uhr laufe und neue Produktivitätsrekorde breche. Der Unternehmer hört das gern, waren die Investitionen doch teuer genug und die Maschinenstundensätze entsprechend hoch. Die Auswirkungen solch falsch verstandener Produktivität sind aber schon nach kurzer Zeit zu spüren: Bestände hinter der neuen Hightech-Errungenschaft, weil die nachgelagerten Prozesse nicht hinterherkommen, Bestände im Lager, weil die Losgröße entsprechend der neuen Kapazitätnach oben >angepasst< und die Anschaffungskosten damit schöngerechnet wurden. Schließlich führt die Neuinvestition auch noch zu einer Verschlechterung der Termintreue, weil die hohen Losgrößen lange Maschinenbelegungszeiten mit sich bringen und andere Aufträge vernachlässigt werden. Kurz: Die neue Anlage ist vermeintlich produktiv; wirtschaftlich aber ist sie nicht, denn ihr Beitrag zum Unternehmensergebnis ist mehr als fraglich. Hohe Zerspanraten allein sind also kein Maßstab für eine hohe Produktivität in der Fertigung. Wenn die notwendigen Rahmenparameter nicht entsprechend angepasst werden, können Neuinvestitionen schnell in einer Investitionsfalle enden. Gerade für den Mittelstand ein Risiko, das auf jeden Fall vermieden werden sollte.
Rahmenbedingungen intelligent aufeinander abstimmen
Welche Rahmenbedingungen definieren nun den wirtschaftlichen Einsatz von Maschinen und Anlagen im Produktionssystem?
Es sind folgende:
- Eine ausbalancierte Prozesskette: Ein Prozess ist nur so schnell wie sein langsamstes Element. Diese Kapazität definiert den Produktionstakt. Ein zu schneller Takt in vorgelagerten Produktionsprozessen führt unweigerlich zum Materialstau.
- Das Wissen um den vorhandenen Engpass: Es gilt zu ermitteln, ob es sich um einen systematischen oder dynamischen Engpass handelt. Ein Engpass muss dabei nicht immer eine Maschine oder Anlage sein. In personalintensiven Bereichen sind es häufig die Mitarbeiter, es können aber auch Werkzeuge sein.
- Die Verfügbarkeit des (Maschinen-)Engpasses: Mit dem OEE (Overall Equip-ment Efficiency) wird gemessen, wie effizient eine Maschine produziert. Aus dem OEE lassen sich organisatorische und technologische Maßnahmen ableiten, die den Engpass entspannen.
- Das Zielsystem des Unternehmens: Die Mitarbeiter müssen Interesse am unternehmerischen Handeln haben. Dabei ist es zunächst nicht entscheidend, ob dies auf ein wert- oder werteorientiertes Führungssystem zurückzuführen ist. Wichtig ist das Zusammenspiel der einzelnen Parameter, die, intelligent aufeinander abgestimmt, ein wirksames Produktionssystem ergeben. Eine ausbalancierte Prozesskette erfordert einen hohen OEE, um die marktsynchrone Produktion - die Fertigung der richtigen Menge zur richtigen Zeit - sicherstellen zu können. Ein hoher OEE ist dabei nicht zwingend über die gesamte Prozesskette erforderlich, am Engpass aber unerlässlich (Bild 1).
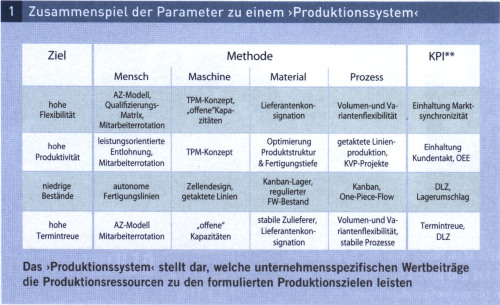
Kennzahlen geben Aufschluss über die Effizienz der Fertigung
In der Praxis haben viele Produktionsleiter häufig nur ein latentes Bauchgefühl, wie effizient ihre Fertigungsressourcen
gerade eingesetzt werden. Zwar wird die Produktivität in vielen Fällen verfolgt, aber Kennzahlen wie interne Termintreue, OEE
oder Flussfaktor - das Verhältnis von Bearbeitungszeit zu Durchlaufzeit - sind häufig Mangelware.
Dabei gibt bei richtiger Anwendung gerade der OEE entscheidenden Aufschluss darüber, was in der Fertigung schief läuft. Definiert
ist der OEE als Anlagenverfügbarkeit x Leistungsfrad x Qualitätsfaktor (Bild 2).

Die Anlagenverfügbarkeit gibt an, welche Zeit die Anglage für die Produktion zur Verfügung steht. In der Praxis stellt sich schon hier häufig die Frage, wie die 100 Prozent definiert werden. Basiert die Verfügbarkeit auf einem 3-, 4- oder 5-Schicht-Modell? Ein zweiter zentraler Faktor, der in die Anlagenverfügbarkeit eingeht, sind Störungen im Betrieb. Auch hier gibt es häufig nur ein Achselzucken, wenn nach einer >Pareto<-Analyse für die Anlagenstillstände gefragt wird. Dabei lassen sich gerade an dieser Stelle wichtige Aufschlüsse ableiten, zum Beispiel über notwendige TPM-Maßnahmen. Auch organisatorische Schwachstellen - >Warten auf Material oder Werkzeug< ist hier der Klassiker - stehen häufig unter den Top 5 der Störgründe und zeigen, wie effizient Anlagekapazitäten eingeplant werden (Bild 3).

Der Anlagennutzungsgrad definiert, welche Menge mit der Maschine in der Zeit ihrer Verfügbarkeit produziert wird. Auch hier gibt es zentrale Stellhebel, die die Anlagenproduktivität beeinflussen. Ein Aspekt, der hier häufig mit Produktionsleitern diskutiert wird, ist das Rüsten. Dieses Thema kommt spätestens dann auf, wenn in der Diskussion um eine marktsynchrone Produktion die Verkleinerung der Losgrößen angesprochen wird. Kleinere Losgrößen ermöglichen es, mehr Varianten in kürzerer Zeit zu produzieren - eine zwingende Voraussetzung für einen optimierten Wertstrom im Kundentakt. Das wiederum bedeutet jedoch, dass mehr gerüstet werden muss, wodurch der OEE zunächst negativ beeinflusst wird. Um dies zu kompensieren, muss der Rüstaufwand deutlich reduziert werden. Beim Finden geeigneter Methoden können Rüstworkshops helfen (Bild 4).

Das technisch Machbare mit vier Alternativen ausschöpfen
Von zentraler Bedeutung sind auch die (genutzte) Maschinenleistung und die im ERP (Enterprise Ressource Planning)
hinterlegten Vorgabezeiten. Hier gibt es in der Regel eine Diskrepanz zwischen den vom Maschinenhersteller vorgegebenen
Parametern (Vorschub, Schnittgeschwindigkeit) und den im Arbeitsplan hinterlegten Bearbeitungszeiten.
Die Ursache für diese Verschwendung liegt meist nicht bei den Mitarbeitern, sondern in technologischen Rahmenbedingungen
wie der Maschinenaufstellung, einer veralteten Maschinensteuerung oder der Auswahl nicht optimaler Zerspanwerkzeuge.
Genau hier aber liegt das unternehmerische Potenzial. Aus Markt- (Termin) und Unternehmersicht (Kosten) ist es
sinnvoll, das technologisch Machbare auszuloten. Für den Unternehmer gibt es in der Regel die vier Alternativen:
- Ersatzinvestition,
- Erweiterungsinvestition,
- Retrofit vorhandener Ressourcen,
- Aufbau externer Kapazitäten.
Ersatzinvestitionen erfolgen in vielen Unternehmen unter falschen Annahmen. So wird eine ROI-Betrachtung gerne genutzt, um die neue Anlage mit hohen Losgrößen wirtschaftlich erscheinen zu lassen. Eine Erweiterungsinvestition wie die Anschaffung einer zusätzlichen, vergleichbaren Anlage bedeutet für das Unternehmen neben dem erhöhten Platzbedarf häufig auch Kapazitätsüberhänge. Durch intelligente Anlagenkonzepte muss diese Kapazität flexibel einsetzbar gemacht werden. Ein Retrofit kann mit wenig Aufwand viel Nutzen bringen. Durch neue Antriebe oder Steuerungen lässt sich die Produktivität vorhandener Maschinen und Anlagen häufig deutlich verbessern. Reduzierte Stillstandszeiten bei schnelleren Bearbeitungszyklen und engere Fertigungstoleranzen sind die wesentlichen Parameter, die den OEE nach einem Retrofit deutlich verbessern. Schließlich kann der Aufbau externer Kapazitäten (verlängerte Werkbank) eine Alternative sein, sobald zuverlässige Lieferanten zur Verfügung stehen und sich das Outsourcing nachweislich rechnet. Die Kunden verlangen heute ein Höchstmaß an Flexibilität. Für das Unternehmen bedeutet dies eine auftragsbezogene Produktion, die volumen- und variantenflexibel die Anforderungen der Kunden erfüllt. Die Reaktionszeit zum Markt ist heute einer der zentralen Erfolgsparameter. Wer diese Zeit nicht ausschließlich über Fertigwarenbestände sicherstellen will, kommt an einer Optimierung der (kundenwirksamen) Durchlaufzeit nicht vorbei. Das erfordert Maschinen und Anlagen mit demnotwendigen Wirkungsgrad. Das bedeutet aber auch, dass man in der Lage sein muss, Auftragsschwankungen zu kompensieren (Stichwort >volumenflexible Produktion<, Bild 4). Kleine, flexible Anlagenkonzepte haben hier deutliche Vorteile gegenüber kostenintensiven Neuinvestitionen. Ein intelligentes Zellendesign, beispielsweise in U-Form, ermöglicht es, zusätzliche Maschinen bei Bedarf zu integrieren und die Kapazität anzupassen. Voraussetzung ist ein flexibles Aufstellkonzept, das bewegliche Maschinen mit einer Medienversorgung >von oben< erfordert. Derartige Anlagen können schnell in andere Linien integriert oder bei Produktneuanläufen komplett neu aufgestellt werden.
Weniger ist häufig mehr
Maschinen und Anlagen im Produktionssystem effizient einzusetzen bedarf einer systematischen Vorgehensweise, die schon
bei der Beschaffung beginnt. Die neueste Steuerung oder mechatronische Werkzeuge sind keine Garanten für die
Wirtschaftlichkeit einer solchen Investition. Die Verfügbarkeit von Maschinen und Anlagen ist zentrale Voraussetzung,
um effektiv auf Kapazitätsschwankungen reagieren zu können. Die Maschinenauslastung allein ist aber kein Maßstab
für eine wirtschaftliche Produktion. Vielmehr muss die Frage im Vordergrund stehen: Wie schnell kann das
Unternehmen auf Marktanforderungen reagieren? Letztlich sind Maschinen und Anlagen als eine Ressource im Produktionssystem
zu sehen, deren Beitrag zur Erreichung der Produktionsziele definiert werden muss. Hieraus leiten sich die Anforderungen
an das Maschinen- und Aufstellkonzept ab. Der Weg führt über eine kombinierte OEE-Betrachtung und Wertstromanalyse,
die in der Fortsetzung des Artikels dargestellt werden.
Am 23. September setzt CIM Aachen in Mainz die Seminarreihe >Produktionscontrolling< fort und thematisiert
unter dem Motto >Potenziale erkennen - Wertschöpfung messen und optimieren< zentrale Aspekte zur Steigerung der
Wirtschaftlichkeit von Unternehmensprozessen.
erschienen in Werkstatt + Betrieb, April 2008